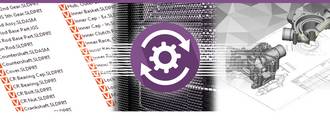
Serveur d'automatisation Kisters (KAS)
Outil de traitement par lots pour une conversion automatisée sans interaction de l'utilisateur
Le Kisters Automation Server KAS est le complément idéal pour tous les composants de la famille de produits 3DViewStation lorsqu'il s'agit d'automatiser des procédures répétitives. Il s'agit principalement de la conversion de données CAD 3D natives en format de données 3DVS léger. Par exemple, une carte Catia de 5 Go, qui prend 5 minutes à charger en mode de chargement natif, peut être chargée en seulement 1 seconde après la conversion au format 3DVS. Toutes les informations peuvent être conservées ou réduites selon les paramètres. La conversion peut être monolithique ou entièrement éclatée, c'est-à-dire dans un fichier 3DVS par fichier de géométrie. Cela réduit considérablement l'effort de conversion après la modification d'une pièce individuelle intégrée éventuellement plusieurs fois. Le KAS peut également être utilisé pour générer automatiquement des vignettes pour les systèmes PLM ou pour exporter toutes les vues qui ont été créées pour un composant dans un format 3D ou 2D ou pour exporter le composant entier dans un format 3D standard.
Parlez-nous maintenant – nous serons heureux de vous conseiller
Nous sommes heureux de vous conseiller
Ventes
+49 2408 9385 517
Les exemples de projets suivants proviennent de nos clients KAS Batch-Tool :
Un fabricant d'hélicoptères convertit toutes ses données CAD natives au format 3DVS avant de les visualiser. La visualisation de l'hélicoptère configuré est ainsi extrêmement accélérée. En tant que monolithe, le temps de chargement est maintenant inférieur à 10 secondes pour 2 à 3 millions de pièces. Le système de CAO n'a jamais été capable même approximativement de charger l'hélicoptère complet.
Un constructeur de camions utilise le KAS pour convertir ses données CAO natives par batch au format léger 3DVS. Certains fichiers sont contrôlés par des métadonnées, et sont en plus également transformés dans BREP. Une fois le camion configuré, il est selon les souhaits du client converti en données STEP partiellement transformé via le KAS, des dessins en 2D sont générés automatiquement.
Une société d'ingénierie d'usine utilise la KAS pour réduire ses quelque 5 TB ( !) Convertir les données CAO au format 3DVS. Il est ainsi capable de charger les données d'une usine d'environ 200 millions de composants avec le 3DViewStation WebViewer.
Un chantier naval utilise KAS pour convertir un navire complet au format 3DVS. Le temps de chargement ultérieur des quelque 10 millions de composants est d'environ 15 secondes pour l'édition VR, mais aussi pour la version de bureau et la version WebViewer.
Notre solution de collaboration : VisShare utilise KAS en arrière-plan pour convertir les données natives au format 3DVS et pour générer des images de prévisualisation.
Prise en charge des formats de fichiers 3D
Extrait :
Importation 3D de données CAO natives et neutres, par exemple :
Catia, NX, Creo, Solidworks, SolidEdge, Inventor, SAT, Parasolid, JT, STEP, 3D PDF, Revit, GLTF, 3DXML, VRML...
Exportation 3D :
STEP, JT, 3D PDF, 3MF, Parasolid, VRML...
Prise en charge des formats de fichiers 2D
Extrait :
Importation 2D de dessins, Office, images :
Catia CatDrawing, NX 2D, Creo DRW, Solidworks slddrw, DWG, DXF, HPGL, 2D PDF, TIFF, JPEG...
Exportation 2D :
DXF, PDF, CGM, PNG, SVG, BMP...
The interacive Kisters 3DViewStation and also batchtool KAS are no classic CAD converters, but can help translating 3D file formats into others and also allow to derive high quality 2D vector or raster drawing and images from the 3D-models.
Translating into a light weight representation like the Kisters 3DVS file format opens new options for 3D-based technical documentation, 3D technical illustrations, 3D assembly instructions, manufacturing, design review, collaboration and more. By staying in the 3D world, processes will become streamlined, the quality of the assets will be increased and a lot of interaction time will be saved.
With thousands of companies using of software we learned, that in many cases like collaboration a translation into a neutral file format could be avoided, if a Web based visualization solution like our 3DViewStation WebViewer version was used.
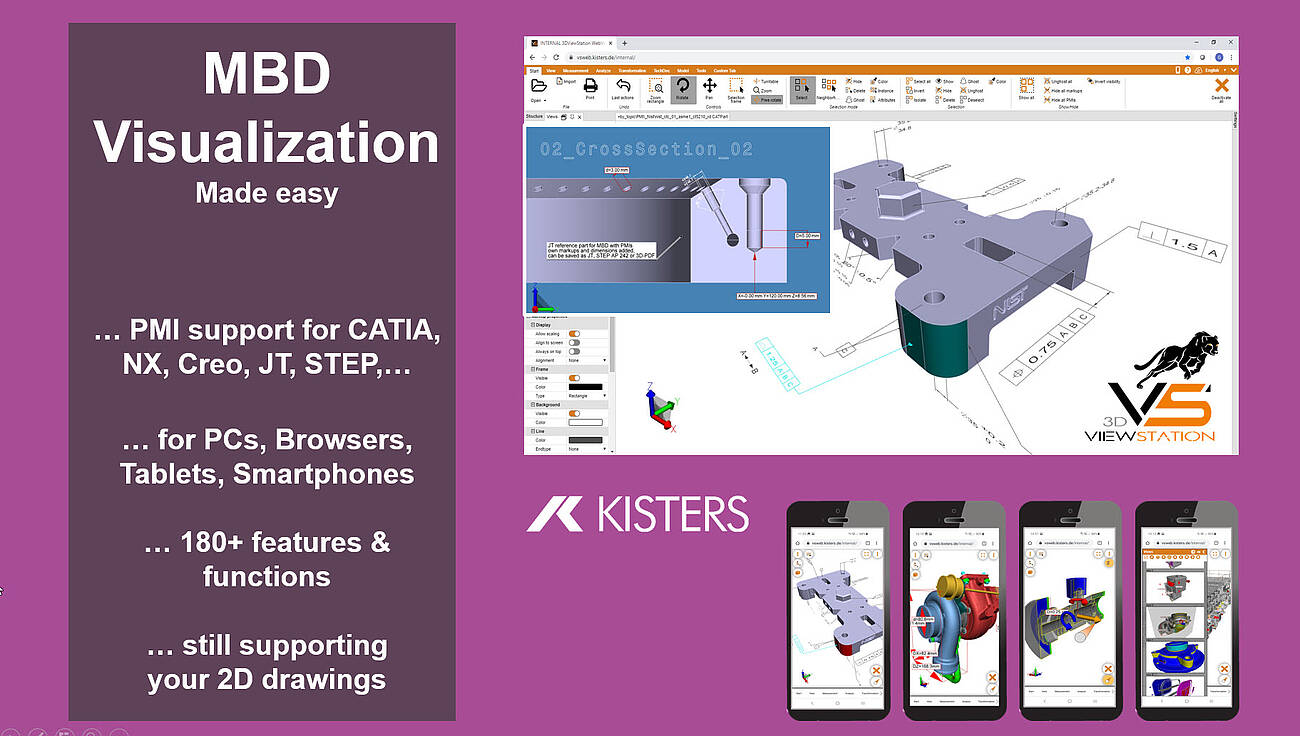
What do I need to know when translating a 3D-CAD model into another neutral 3D file format?
We think, that there are several important considerations to keep in mind, like file format selection, model structure, views, annotations, metadata and more:
So first of all, we need to choose an appropriate neutral 3D file format for the translation. The most important neutral BREP file format for sure is STEP (Standard for the Exchange of Product Data). Here typically AP 214 and AP 242 are used. In the automotive industry JT has become an important standard. Less important, but still used is IGES (Initial Graphics Exchange Specification). Finally there are several rather simple tessellation based file formats like STL (Standard Tessellation Language), VRML (Virtual Reality Modelling Language) and OBJ, see also our complete file format list, section export 3D. The specific format you choose will depend on the requirements of the receiving software or system. BREP based file formats are intended to exchange between CAD systems, while tessellation based file formats are good for many visualization needs.
In most cases we need to take into account the structure and hierarchy of the original CAD model and how it will be translated into the neutral file format. CAD models often have an organized structure with components, assemblies, and sub-assemblies. Ensure that the translation process maintains this structure for better organization and future editing or manipulation. Be aware, that some file formats do not support the structure and hierarchy.
Many 3D-CAD systems support so called captures or PMI views, which are all called views in the 3DViewStation world. As not all file formats support such views, you we might have to select the right one, if we need to retain them.
If your enterprise follows the MBD concept (Model Based Definition, also called 3D Master), then you replaced 2D drawings by 3D annotated models. Translating such files requires a target file format, which will support PMIs (Product Manufacturing information). STEP AP 242 and JT are such file formats. When using Kisters 3DViewStation or KAS in order to translate these files, you need to ensure, that the correct import and export settings have been set.
Today it is very important to preserve metadata, attributes, and properties associated with the CAD model, such as material information, part numbers, or custom properties during the translation process. Be careful: Some formats may support metadata transfer, while others may require additional steps or custom scripting, some file formats might not even support any.
We, the visualization experts, are aware of how visual properties, such as colors, textures, or surface finishes, will be handled in the translation process. Some neutral file formats may support these visual attributes, while others may require additional steps or settings to preserve or recreate the desired appearance in the target application.
We also need to understand the level of geometry accuracy and detail required for the translation. Different file formats may handle geometry representations differently, such as using NURBS (Non-Uniform Rational B-Splines) or polygonal mesh representations. Consider the level of precision and detail needed for your intended application and ensure the chosen file format supports it.
We need to confirm that the units and scale of the original CAD model are correctly preserved during the translation. This is crucial to ensure dimensional accuracy and proper scaling in the resulting neutral file format. Verify that the translated model aligns with the intended unit system and scale in the target application.
In case we know the target system we do have a chance to understand the compatibility and limitations of the target software or system with the chosen neutral file format. Different software packages or systems may have varying support or interpretation of specific file formats. Ensure that the target application can correctly read and interpret the translated file for optimal compatibility and usability. We can help selecting the most promising file format depending on the target system.
While KAS allows to translate file in batch mode, you can use 3DViewStation Desktop or WebViewer version to do these translations manually. But they are also good to review the translated model to confirm its accuracy and integrity. Check for any errors, missing geometry, or unexpected changes that may have occurred during the translation process. There are also quality checkers available on the market, which might be used before forwarding the file or before importing them into the target system.
When talking about 2D exports, first of all we should mention, that it is no trivial task to derive a full scale, high quality, still small 2D vector representation for a 3D CAD model. At the same time generating an image, like a thumbnail preview of even a high resolution image is rather easy.
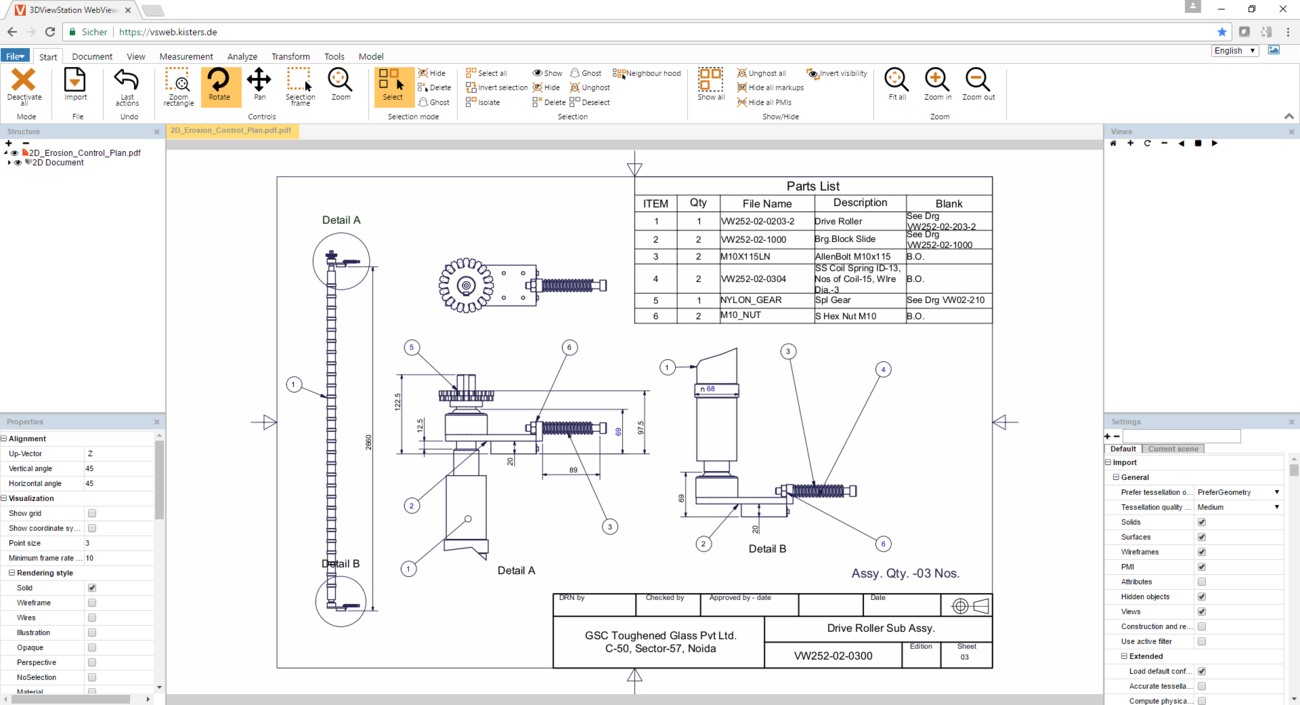
Why does someone want to export a 3D-CAD model to a 2D vector drawing?
There are several reasons why someone may want to export a 3D CAD model to a 2D vector drawing:
Many manufacturing processes still rely on 2D representations, especially for certain types of fabrication, such as laser cutting, CNC machining, or sheet metal bending. Exporting a 3D CAD model to a 2D vector drawing allows manufacturers to generate the necessary cutting or machining paths, specify part dimensions, and determine material requirements.
In some industries, older software or equipment may only support 2D vector formats. Exporting a 3D CAD model to a 2D vector drawing allows compatibility with such systems, enabling data exchange or integration with existing workflows without the need for complex conversions or software upgrades.
In certain contexts 2D vector drawings can be useful for visualizing a design. For example, in architectural or interior design, 2D floor plans or elevations provide a comprehensive view of the space, including the layout, dimensions, and other architectural details. These drawings are often easier to understand and work with for certain design-related tasks.
2D vector drawings are commonly used for documentation purposes. They provide a clear and detailed representation of the design, including dimensions, annotations, and other important information. These drawings can be shared with stakeholders, such as manufacturers, contractors, or clients, for better understanding and communication.
Today 2D vector drawings are often used for 2D technical illustrations, 2D assembly instructions, or 2D user manuals, mostly provided as 2D PDF file or printed documents. By exporting a simplified 2D representation of a 3D CAD model, complex designs can be visually broken down into clear, step-by-step instructions, aiding in the assembly, maintenance, or operation of a product or system.
In some cases, a 2D vector drawing may be preferred for design review or collaboration purposes. By simplifying the representation to 2D, it becomes easier to focus on specific aspects of the design, such as individual components, dimensions, or structural details, without the complexity of the 3D environment. This can facilitate discussions, feedback, and design iteration.
By exporting a 3D CAD model to a 2D vector drawing, individuals can leverage the benefits of both formats, combining the rich detail and accuracy of the 3D model with the clarity, simplicity, and compatibility of the 2D vector representation for various applications.
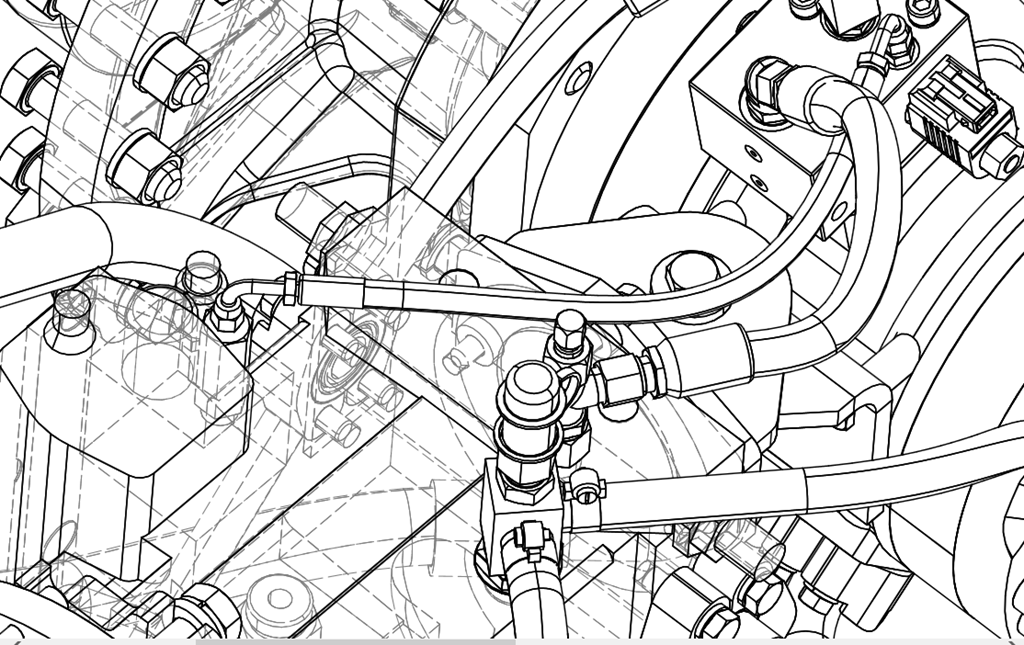
What do I need to know when exporting from a 3D-CAD model to a 2D vector file?
Determining the appropriate file format for the vector file is key. In the manufacturing industry common file formats used for 2D drawings include 2D DXF (Drawing Exchange Format), 2D PDF (Portable Document Format) and SVG (Scalable Vector Graphics). Sometimes the file format required depends on the target application and system, where it will be used.
Organize your CAD model into appropriate layers and/or blocks before exporting. This allows for better control over different components, annotations, or visual elements in the vector file. 3DViewStation APIs and our batch tool KAS allow to automatically build layers and blocks, based on the product structure of the 3D-CAD model.
Familiarize yourself with the export settings and APIs provided by 3DViewStation and KAS. These settings may include options for curve smoothing, resolution, and compatibility with different software or devices. Decide whether you want to include hidden lines in the exported vector file or show only visible lines. Depending on the purpose of the 2D representation, you may need to enable or disable hidden line removal to accurately represent the design.
3DViewStation and KAS can help you simplifying or optimizing the geometry of your 3D CAD model before exporting to a 2D vector file. They allow to remove unnecessary details, such as internal components or hidden features, to keep the resulting vector file clean and lightweight. This can help improve performance and reduce file size.
Consider the desired level of quality and precision in the exported vector file. This relates to the smoothness of curves, accuracy of angles, and overall detail. Higher quality settings may result in larger file sizes, so balance your requirements with file size considerations. Very often it is crucial to keep file size as small as possible, which requires intelligent vectorization and compression algorithms, like 3DViewStation and KAS provide.
We need to ensure that the dimensions of your 3D model are accurately translated to the 2D vector file. Check the scaling and units of measurement to avoid any discrepancies. File formats like PDF know their paper size, which might make it easier to retain the intended scale during the conversion.
Leveraging 3DViewStation Desktop or WebViewer version you can verify that the exported vector file represents the desired geometry and level of detail. Pay attention to curves, arcs, and splines, as they may require higher resolution or special settings to maintain smoothness.
Some file formats do support line thickness and styles. As 3D CAD model do not have any settings like that, we’ll need to specify them in such a case. Different software may handle linework differently, so be prepared to adjust these settings during the export process.
3DViewStation and KAS will care for colors and fills automatically, depending on black & white or color setting: You can assign specific colors to different layers or components, interactively or via API or opt for a monochromatic representation during export.
Finally, if your 3D CAD model includes 3D annotations, labels, dimensions, balloons, tables or text blocks, verify that they are appropriately exported and legible in the 2D vector file. These annotations are essential for conveying important information about the design and can aid in manufacturing or construction processes.